September 1, 2009
Searching for the Extreme: Richard Vandersteen of
Vandersteen Audio: Part One
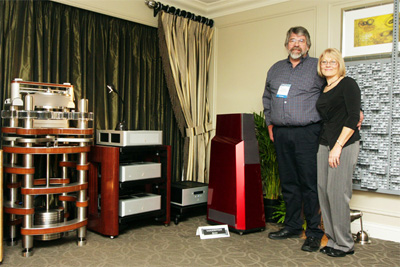
Richard Vandersteen and his wife Eneke at CES 2009.
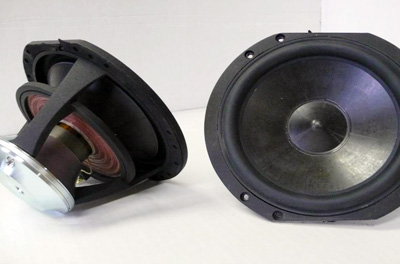
Vandersteens 7.25" Scan-Speak Illuminator midbass driver, featuring an
aerodynamic neodymium magnet system and proprietary cone of carbon-fiber-and-balsa
composite.
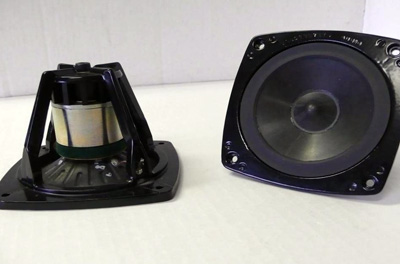
Vandersteens open-basket 4.5" midrange driver (patent pending), now
incorporating the carbon-fiber/balsa composite cone.
|
Richard Vandersteen is the founder,
principal, and guiding light behind Vandersteen Audio. For the past 33 years, Vandersteen
Audio has provided sonic enjoyment to audiophiles and music lovers throughout the world.
Given that more than 250,000 Vandersteen Model 2 loudspeakers, in their various
iterations, have been sold to date, its arguable that no other individual has had a
larger impact on the world of high-performance audio than Richard Vandersteen.
For the past ten years, Vandersteen has been on a quest to
create the ultimate drivers for a new statement speaker system, his Vandersteen Model
Seven. Shown to the public for the first time at the 2009 Consumer Electronics Show, the
prototypes of the Seven made quite an impact. I visited the Vandersteen Audio design and
production facility in Hanford, California. There I watched the new drivers cones
being made, and Model Seven cabinets being assembled. The highlight of the day, however,
was listening to album after album through the Model Sevens on Richard and Eneke
Vandersteens reference system, then discussing with Richard the technical aspects of
his flagship. My Dictaphone was on; here is our conversation.
Pete Roth: Vandersteen Audio has focused
extensively on driver technology through much of its history, but the Model Seven seems to
explore new territory. What are your thoughts about the driver technology youre
working with in the Seven?
Richard Vandersteen: Its always been my goal
to have -- we call it "perfect piston" -- to have perfect piston operation at
least an octave beyond the frequency range we want the driver to work in. In a perfect
piston, all parts of the diaphragm -- the cone -- are moving exactly in unison, from the
edge all the way to the voice-coil. Attached to such a cone, the voice-coil can in turn
energize the air in the room exactly as it is intended by the drivers magnet system
and the current coming from the amplifier.
To achieve this is incredibly demanding -- very, very
difficult. Not so much for a midbass woofer, because if youre crossing over at 600
or 700Hz, youre only looking at needing good behavior to a couple of kHz. (Our first
breakup mode in our new midbass woofer is actually around 10kHz, so that driver easily
achieves our perfect piston requirements to about four octaves out.) But, with regard to
the midrange, because we use time- and phase-correct crossovers (first-order filters), by
crossing over at approximately 5kHz wed need a midrange to have good behavior to
10kHz -- and preferably, as that is just one octave, [we] would like to have more than
that. In our case now, the midrange drivers first breakup is at 15kHz, which is well
out of the way, is well attenuated, and without high "Q" -- it is low
"Q" -- with not that high of a peak to begin with.
With other materials -- aluminum, for example -- its
not uncommon to have the "Q" of the peak be very narrow, yet 15-20dB in
amplitude. This is very difficult to deal with, and you are then forced to use very steep
filters that ring like dinner bells all by themselves, to compound the ringing that is in
the diaphragm or the driver. To use first-order filters to try to notch out a peak like
that, so narrow in "Q" and high in amplitude, is virtually impossible to do
passively, which is our preference.
PR: So with regard to your new drivers, and the
patent pending behind them, the most unique story lies in their balsa-wood cores. Why, in
a nutshell, did you settle on balsa as the core material for the Model Sevens
midrange and midbass cones?
RV: Because its compressive strength is the single
strongest material by weight available, and it also happens to be a very good damping
agent for resonance control.
PR: Explain the particular type and grade of
balsa you use.
RV: We use the balsa in an end-grain orientation,
where it has its best compressive strength. Balsa wood is available in all different
weights, graded by weight in pounds per cubic foot. Balsa wood can range all the way from
3.5 pounds per cubic foot to 20 pounds per cubic foot. We buy nothing but the
"ultra-lightweight" grade, but there is very limited supply. From an entire
container that comes in from Ecuador, there may be only 3 or 4 cubic feet of the
ultra-lightweight material. All of the balsa we use in the midrange cone is 4.5 pounds per
cubic foot or less. For the 7.25" midbass driver, we use the material graded between
5 and 6 pounds per cubic foot.
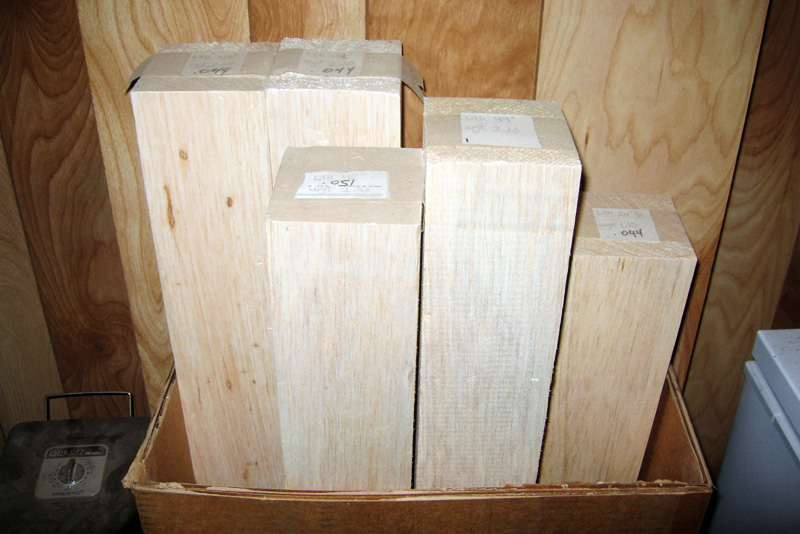
4" x 4" blocks of ultra-lightweight balsa
wood awaiting processing.
PR: How much balsa do you need to process to get
what you need?
RV: We start off with way more than we ultimately
need, given the difficulty of machining it. Through our patented process, we stage the
various steps of machining in order to handle it. We end up throwing 90% or more of the
material away. But each midrange starts with a 4" x 4" x 1.25" piece, from
which the cone is machined out. We segment four pieces together to create the 6" x
6" x 1.5" block from which the midbass cone is machined.
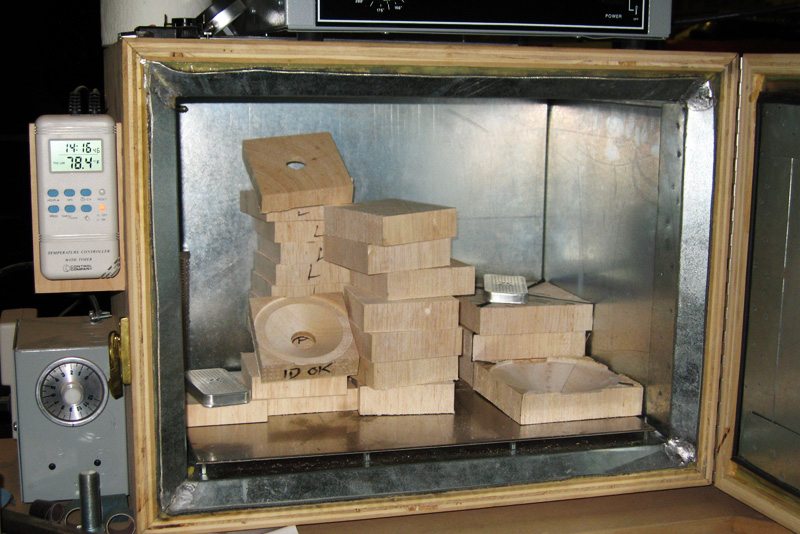
Balsa cut into 4" x 4" x 1.25" blocks,
from which the driver cones are machined, "baking" in a special oven to remove
all residual moisture -- a necessary step to ensure proper lamination of the cone skins of
ultra-high-modulus carbon fiber.
PR: How did you identify balsa as a material to
use?
RV: From my airplane hobby, really, knowing that
balsa was incredibly strong. At first, I didnt realize how well balsa would work in
a constrained-layer-damped scenario, but I did know that it was very lightweight. As it
turns out, its compressive strength at those light densities is unmatched by the
alternatives. For example, the balsa graded at 4.5 pounds per cubic foot has a compressive
strength of 680psi, while Rohacell of the same weight per cubic foot has a compressive
strength of just 215psi. While these materials compressive strengths increase with
density, Rohacells compressive strength nevertheless tops out at about 500psi, well
short of the balsa we use. And when heavier core materials are used, much of the benefit
of the increased compressive strength is merely offsetting the weight penalty incurred. So
the balsa is clearly superior.
PR: What other options for materials did you
explore?
RV: Ive been experimenting with the creation
of these cones for going on ten years now, so Ive looked at all kinds of materials.
I investigated so many different structural foams -- extensively used in the aircraft
industry, in particular -- as well as all of the various honeycomb materials (Nomex,
Hexcell, etc.), which are oriented like a beehives cells. Many of these have good
strength, but in high-vibration environments can be very difficult to bond a skin to
without weight getting in the way, as they necessitate excessive epoxies in the layup in
order to completely bond the skin to the ends of the materials. Under long-term
destructive testing of such alternative materials we saw a lot of delamination problems,
although some have been effectively used in the audio industry, primarily in woofers.
PR: As a core material, how different is balsa
from Rohacell, which has found multiple uses in audio?
RV: Rohacell is a structural foam that has become
quite common in the audio industry and, obviously, the aviation industry, from which it
first gained notoriety. In fact, I used Rohacell extensively in building my airplane.
Nevertheless, I measured the compressive strength of balsa to be about three times that of
Rohacell. You see, the function of the core material in a carbon-skinned composite
sandwich is not simply to hold everything together (to get a spacing between the front and
the back carbon layers), but also to form the truss. It is through this truss that you get
the desired rigidity. In order for that to be obtained and optimized, it needs to be
lightweight and have excellent compressive strength.
Balsa has a much greater anti-resonant quality than
Rohacell, other structural foams or the honeycomb materials. As a matter of fact,
Ive just learned that the new Corvettes use balsa and carbon fiber for the floor
panels, and while Im sure it has something to do with weight (although its not
a race car), I read that the main reason General Motors engineers it into the Corvette is
to attenuate road noise -- in other words, for its damping characteristics.
PR: How do balsas antiresonant qualities
manifest themselves in the drivers?
RV: By its low "Q" resonance. A very high
"Q" resonance simply means that there is a narrow band of frequencies, but very
steep and with high amplitude. A low (also called a wide) "Q" resonance would
involve more frequencies, but the amplitude is considerably lower. Of course, if a
resonance has no bump at all in its response (no amplitude), that is considered
"critically damped," and you can approach that with balsa. On its own, balsa
results in a very damped resonance of 4-5dB. It looks like a low foothill, not a mountain,
and is very easy to deal with, especially when its way out there, over an octave
beyond the crossover point. We go ahead and notch the bump out with our crossovers anyway,
to eliminate any residual effects of the resonance.
A lot of people dont realize that common paper cones
-- even sophisticated ones with some carbon fibers sprinkled in the matrix -- and
plastic-type cones normally used in a 6.5" woofer or a 7.25" woofer, typically
have their very early signs of resonance (entering into their first breakup modes) at as
low as 300 or 400 cycles. Even at such low frequencies, the cones are becoming chaotic and
no longer act as a perfect piston.
PR: What is the nature of your patent?
RV: Basically, the patent is about using a balsa
core with carbon-fiber skins in a midrange cone -- defined as a cone 5" or smaller in
diameter. It also includes some process elements, as they are rather unique -- but one
never knows, as you go through the "pending" progression, how much of the actual
process will be allowed to remain in the final patent.
PR: What different types of carbon fiber are
there to choose from for the skins of the new cones?
RV: There are several common carbon-fiber types used
in loudspeakers today. The first is the normal woven carbon fiber, which you see on car
hoods these days -- on everything, really. In this standard type, the strands are woven
up, over, and under in what are called tows or groups, and they cross at 90 degrees.
Thats the standard carbon fiber that I used to build my airplane. It is used for
lots of things today, and comes in different varieties: twills, weaves, 1K tows, 3K tows,
6K tows, etc.
Then you have the unidirectional-fiber type. Again, the
fibers are all carbon, but instead of a weave, all of the strands lay in the same
direction, so you have maximum strength in one direction and virtually no strength in the
other direction. The lowest-cost alternative used in speakers today is a random fiber,
called a veil, which you can get in various weights. The fibers are spun in totally random
arcs and curves, going in all directions, and can be laid up in various layers. We played
with that years ago. It was the first material we used and the easiest to work with, but
not very stiff or strong, although it makes a good finish.
The other thing that matters with carbon fiber, whether you
use a pre-preg or wet layup, is the modulus strength of the actual fibers. There is a lot
of variation there. Standard carbon fibers have a modulus stiffness rating expressed as
about 33 million psi. Weve experimented with uni-fibers with 42 million, 60 million,
and as high as 120 million psi. The present cone material we use is what is called
"ultra-high-modulus" carbon fiber -- its very difficult to get, being used
primarily in satellites.
Then there are various different epoxies or matrices that
you hold this fiber together with. It is the available high-modulus binders with nanotubes
that we utilize. Our tweeter dome also uses the ultra-high-modulus carbon fiber and
high-modulus binders, with the carbon fibers laid-up and layered in a unique fashion to
achieve the rigidity we are looking for, so that the inevitable first breakup mode occurs
over an octave above audibility. So, although pretty bizarre, these materials and
configurations are what it has taken in order to achieve a perfect piston at all
frequencies with at least one octave of headroom, and preferably two octaves or more.
This, in turn, allows our use of first-order filters -- the only option if you are making
time- and phase-accurate speakers. The ultra-high-modulus fiber, high-modulus pre-preg
variety that is in our cones is very expensive and very hard to get, but it really does
the trick. When I asked the manufacturer who else uses the stuff, he told me it is only
used in satellites and by this crazy speaker guy: me.
The only real problem with our resulting cones is the cost.
The cones for the midrange driver cost something like $2000 a pair, which is basically an
order of magnitude more than what otherwise-available, top-quality midrange drivers cost,
with all subcomponents included. But the distortion is so incredibly low, there is just
nothing like them.
End of Part One. Part Two will appear next month.
. . . Peter Roth
peter@ultraaudio.com
|